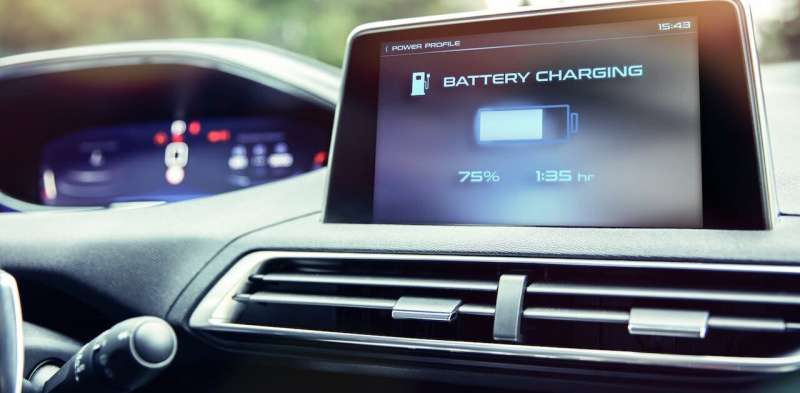
Batteries in electric vehicles have more mileage in city driving rather than highway driving
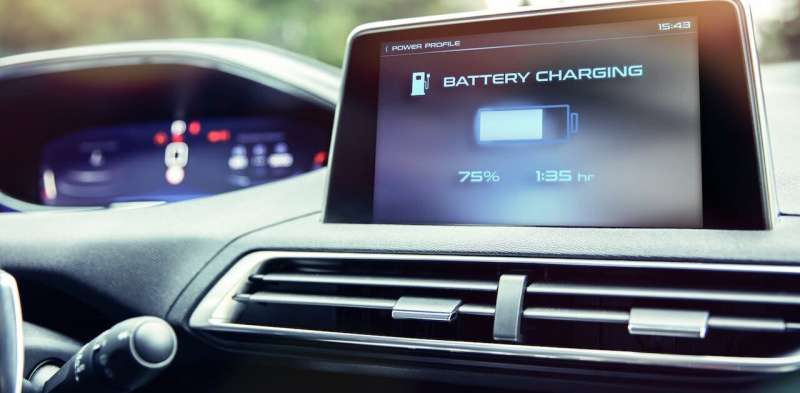
News and Information
July 2, 2023 By Editor
July 1, 2023 By Editor
After years of outsourcing manufacturing to China, countries are finding that their pools of talent have dried up. Just as they’re looking to produce their own batteries and rare earth permanent magnets—both critical for electric vehicles—they don’t have the skilled professionals for the job.
Japan is no exception in this regard—but it now has a plan. The government aims to train 30,000 more battery-related workers by 2030, which would quadruple the industry’s labor force from its current base of 10,000.
To find and train these additional tens of thousands of battery engineers, designers, and technicians, Japan plans to tap high schoolers, as well as students at colleges and vocational schools, recruiting them for multi-year intensive training programs nationwide, according to Nikkei Asia. The first cohort of 40 students will begin learning battery technology in December, at a vocational school in Osaka, Nikkei Asia reported. Then the program will be expanded to high schools, vocational schools, and universities.
Even though Japan was the site of groundbreaking innovations that led to the lithium-ion battery as we know it today, and even though, at its height, Japan commanded over 50% of the global lithium market share, the country now faces a shortage of talent for battery-related work.
The story is the same across many developed economies. The EU expects its battery sector alone will need 800,000 people to be trained or re-skilled by 2025. South Korea’s battery giants have warned of a skills gap that will slow down transition to electric, zero-emissions transportation. And in a sign of how fierce competition is among EV makers for talent, Tesla has said it finds itself paying “CFO-like” salaries to attract battery engineers.
Over in the US—another center of pioneering work on lithium batteries—companies and the government are also urgently trying to fill the battery industry skills gap. In March, the Department of Energy and the carmaker Stellantis teamed up to launch the Battery Workforce Challenge, which includes vocational training and a three-year engineering competition designed to build skills and build a pipeline of battery workers.
Batteries aren’t the only climate technology facing a talent crunch. The rare earths industry is also starved of engineers across the supply chain, from mining and refining to manufacturing permanent magnets, which are needed to drive EV motors and wind turbines.
In a report published last month on China’s rare earths industry, written by industry experts and submitted to Congress and other US government bodies, the authors estimated that China has more than 12,000 full-time rare earths researchers in its national labs, research facilities, and universities. The US, on the other hand, has as few as 300.
June 30, 2023 By Editor
As the aviation world looks to battery-powered planes to help sustainability, the rail sector has been quietly working on a faster alternative. Enter Europe’s first battery-powered trains.
A 20-strong fleet of Hitachi Masaccio trains is now running in Italy, where they are known as “Blues.” It’s the first phase of a 1.23 billion euros project which will add 135 battery-powered trains to national operator Trenitalia’s network, running in Calabria, Friuli Venezia Giulia, Lazio, Tuscany, and the islands of Sicily and Sardinia.
In Calabria, the trains are running on the Ionian Coast, while Sicilian routes include Messina to Palermo and Messina-Catania-Syracuse. Of course, not all the trains on these lines will be the Blues, so it’s pot luck which travelers end up on.
The three- and four-carriage, 300-seater trains are hybrid, working on battery, electric and diesel power. “It is the first time that batteries are used as the main energy source on a fleet of trains for commercial use in Europe,” Trenitalia said in a statement.
The fleet – made with 93% recyclable materials – will cut carbon emissions and fuel consumption by 50% versus diesel trains, Hitachi said in a statement. And by running on batteries through urban areas, they can also eliminate emissions and reduce noise pollution. A “driver advisory system” also suggests the optimal speed to reduce energy consumption.
The trains have a short range of up to 15 kilometers (about 10 miles) on battery alone, but can recharge as they go, using the pantograph (the apparatus on top of the train which connects it to a power line) or by braking, meaning it can recharge multiple times during a journey. Maximum speed is 160 kph (100 mph).
They are also slung at platform level to allow no-steps entry for travelers with mobility issues.
Europe’s rail network is ever expanding, but nearly half – 40% – of the continent’s lines have yet to be electrified, and more than half the trains are powered only by diesel, according to Hitachi.
Some lines face an uphill battle to electrification because of their geography. In Italy alone, there are over 2,500 miles of track that has not yet been electrified – with Hitachi claiming that the Masaccio line offers “an immediate solution to help decarbonize European passenger rail.”
The next model of the Masaccio is due in two years time. It is predicted to run on batteries only, with a journey range of over 100 kilometers (62 miles). Hitachi also plans to retrofit the trains that have only just debuted.
June 29, 2023 By Editor
Global miner Rio Tinto is setting up a battery test plant at an Australian research hub to better understand how its minerals can work for battery makers, an executive said on Wednesday.
Rio set up its battery materials business in 2021 before buying the Rincon lithium mine in Argentina the following year. It has put on ice its plans to develop a large lithium mine in Serbia, for which research and development was centred at its Melbourne research hub, due to community opposition.
“I have just spent some time at Bundoora, where we are constructing an end-to-end battery laboratory to improve our understanding of battery production, manufacturing and chemistry,” said Sinead Kaufman, chief executive of its minerals division.
“At this lab we will build our own batteries, allowing us to test how our minerals and other products will perform in real-world applications, such as in an electric vehicle batteries,” she told a mining conference.
Kaufman said demand for lithium is expected to grow five-fold out to 2030, with a significant supply-demand deficit expected from the second half of this decade.
The battery plant is expected to be operational by November.
June 28, 2023 By Editor
California-based Rondo Energy and Thailand’s Siam Cement Group are going to operate the world’s largest battery factory in Thailand.
The production capacity of Rondo Heat Battery storage at Siam Cement Group’s factory is going to be ramped up from 2.4 GWh to 90 GWh per year – that’s larger than any existing or planned battery manufacturing factory worldwide.
The existing 160,000 square meters (1.72 million square feet) factory is going to be expanded. A spokesperson told Electrek that the launch timeline is over the next few years, but the two companies have not yet committed to a set date.
The 90 GWh of planned capacity will result in 12 million tons of CO2 emissions savings annually, equivalent to removing over 4 million ICE vehicles from the road each year.
Siam Cement Group is the largest and oldest cement building material company in Southeast Asia. Its subsidiary SRIC produces refractory bricks. Also called fire bricks, refractory bricks are made of fireproof materials that can withstand high temperatures.
Each brick that Siam Cement Group makes for Rondo’s batteries (pictured above) is 500 kg and stores 100 kWh – as much as a Tesla Model X.
Rondo Energy, which is backed by Bill Gates-founded Breakthrough Energy Ventures and utility-backed Energy Impact Partners, launched its first commercial operating unit at an ethanol plant in Pixley, California, in March.
The Rondo Heat Battery captures intermittent electricity from solar and wind, stores the energy from that electricity as high-temperature heat in brick materials, and delivers the stored energy on demand as high-temperature heat and/or electricity:
The battery is made only of brick and iron. It charges in as little as four hours and stores heat energy at temperatures up to 1500° C for hours or days, delivering zero-carbon heat for such processes as steel, cement, and chemical manufacturing.
Rondo has designed its battery for such industries as steel, cement, grid energy storage, power plant conversion, and mining.
Here’s how Rondo says its batteries can reduce emissions in different sectors:
Raymond James energy analyst Pavel Molchanov said in a statement:
Electric thermal energy storage can play a useful role in addressing the needs of the industrial sector, which has been slow to decarbonize.
And, from an energy security standpoint, it is worth noting that this technology avoids the use of scarce and expensive materials.
Industry uses more energy than any other sector in the world, and most industrial energy is used as heat. Industrial heat consumes a quarter of total world energy and today releases a quarter of the world’s carbon dioxide emissions.
June 27, 2023 By Editor
General Motors (GM) announced a new deal with Australian-based supplier Element 25 on Monday to expand manganese sulfate production in the US, a key EV battery component.
Under the supply agreement, Element 25 will provide GM with up to 32,500 metric tons of manganese sulfate annually to help the automaker hit its goal of producing over one million EVs in North America by 2025.
The deal also includes an $85 million GM-funded loan to help Element 25 fund the construction of a new battery-grade manganese sulfate facility in Lousiana, expected to be the first of its kind.
Starting in 2025, Element will produce manganese sulfate at the facility by processing manganese concentrate from its mining business in Australia.
Doug Parks, GM executive vice president of global product development, says the Lousiana plant is significant as it’s expected to be the first of its kind in the US to produce battery-grade manganese sulfate. Parks added:
GM is scaling EV production in North America well past 1 million units annually and our direct investments in battery raw materials, processing and components for EVs are providing certainty of supply, favorable commercial terms and thousands of new jobs, especially in the U.S., Canada and free trade agreement countries like Australia.
Element 25 expects to begin site preparation for the 230,000 square-feet facility in the third quarter of 2023, creating around 200 permanent jobs once opened in 2025.
The news comes weeks after GM revealed it would increase its investment (to over $1 billion) in its new cathode factory in Ontario, Canada.
GM says the new funding will help increase cathode active material (CAM) production and its precursor materials (pCAM) needed to manufacture it in North America.
CAM is a key EV battery material consisting of lithium and a secondary metal (or metals) that drives around 40% of EV battery costs. The two most popular today include nickel-cobalt-manganese (NCM) and lithium-iron-phosphate (LFP).
In addition to manganese, GM also secured nickel and cobalt supply after a strategic investment in Queensland Pacific Metals last October, another Australian-based supplier.
After announcing plans for its fourth EV battery plant in the US earlier this month, GM and its JV partners are installing 160 GWh of domestic battery cell manufacturing capacity.
After selling over 20,000 EVs for the first time in a three month-span in Q1, GM forecasts to be on track to build another 150,000 in North America by the end of the year. By mid-2024, GM expects to make around 400,000 EVs in North America as it looks to reach one million annual production in 2025.
The automaker expects a breakout year with the launch of the Silverado EV, Blazer EV, and Equinox EV by the end of 2023.