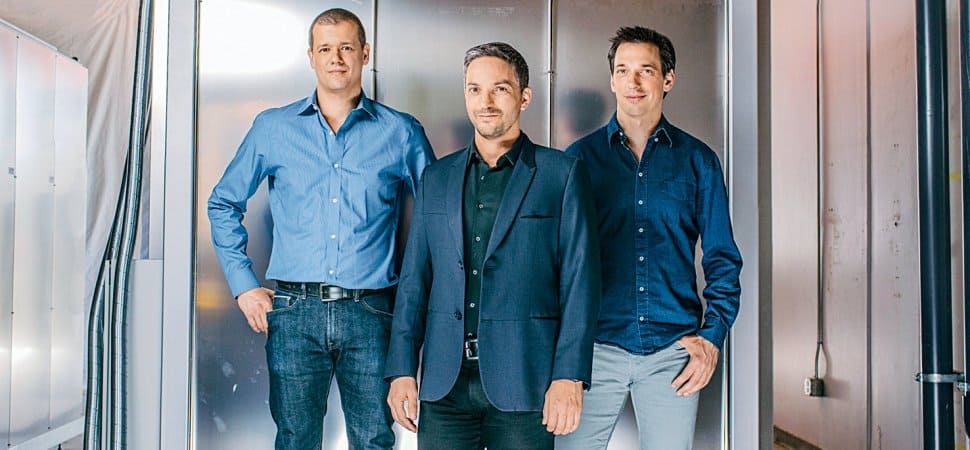
When Gene Berdichevsky and Alex Jacobs moved into a rented house in Atlanta in September 2011, they figured it would be six months, maybe nine, before they’d made enough progress on their startup road map to return to the San Francisco Bay Area in triumph.
They were off by only a couple of years.
One of Tesla’s earliest engineering leaders, Berdichevsky wanted to make a new kind of lithium-ion battery, one that would represent the first meaningful advance in power storage in more than 20 years. By using ultra-efficient silicon rather than graphite to store the ions that provide the charge, he believed his company, Sila Nanotechnologies, could accelerate the world’s transition to renewable energy.
Berdichevsky knew companies like his were a standing joke among battery makers. The industry had learned to tune out startups touting breakthroughs that never quite materialized. “Everyone in this business is rightfully jaded because most of it doesn’t work at the end of the day,” he says.
But he believed Sila had a secret weapon: Gleb Yushin, a materials scientist and Russian immigrant who’d already done much of the underlying theoretical work in his lab at Georgia Tech. Yushin was the reason for the move.
Berdichevsky was right. This summer, Sila’s silicon-based lithium-ion batteries will be powering small devices such as Samsung’s smart watches. As it scales up production at its Alameda, California, plant, Sila will begin delivering batteries that boast an instant 20 percent boost over the status quo, for use first in cell phones and then in cars. To battery makers who’d been struggling to eke out 1 percent annual performance gains, 20 percent “is like levitation, you know?” Berdichevsky says.
But if the end result is wizardry, getting there was more like digging a tunnel with a teaspoon. Nine months after their Atlanta move-in, progress was nowhere in sight. Nailing the physics and the chemistry would demand three full years. And even that, in a way, was just the beginning. Back in the Bay Area, another four years of engineering, validation, and factory design would be required before Sila Nano had a product to sell.
The Magic Sand
That product is not much to look at–just a fine-grained black silicon powder that could be soot or gunpowder. But painted in layers on the anode part of a lithium-ion battery cell, this magic sand stores 24 times more positively charged lithium atoms per atom than the graphite it replaces. That translates to batteries that will extend the range of electric vehicles without recharging by 20 percent–and Berdichevsky expects to double that margin to 40 percent before long. At that level, it could reduce the battery load and thus the price of EVs–something Tesla and other car companies are desperate to do.
At Tesla, Berdichevsky saw battery cost and performance as a bottleneck holding back mass adoption of EVs, which are otherwise a slam dunk for owners: safer, quieter, cheaper to operate. And they don’t emit CO2. Make them cheap enough and “the world gets better very quickly,” he says. Where Elon Musk sought to meet that need by constructing a massive battery plant in the desert dubbed the Gigafactory, Berdichevsky recognized an opportunity to improve the fundamental technology.
Nano Visionary
Yushin’s work represents a sort of battery engineer’s holy grail: devising a way to store lithium in silicon rather than graphite. In a lithium-ion battery, lithium ions, which are atoms stripped of an electron, migrate from the cathode to the anode during charging. It takes six atoms of carbon, the element in graphite, to store one lithium ion, whereas one atom of silicon can hold four lithium ions, making it 24 times as efficient. The problem is that those extra lithium ions cause the silicon to physically swell, and swelling and shrinking repeatedly causes batteries to do nasty things like leak, catch fire, and die prematurely.
Yushin’s answer was to surround the silicon atoms in a nanoparticle scaffold, an engineered molecular structure that provides extra space to store the lithium while maintaining the overall structure’s volume. It was an elegant solution, and, in Yushin, Berdichevsky found a partner for the long journey from the lab to the market.
The nice thing about being a company that takes on technical risk rather than market risk is once you work out the science, that’s pretty much the ball game. Berdichevsky’s biggest concern these days is how fast he can build production capacity to meet incoming demand. “Companies that fail are the ones that solve the easy problems first because they want to show their investors they’re doing something,” he says. “Our philosophy was to solve the hardest problems first.”Volume 90%