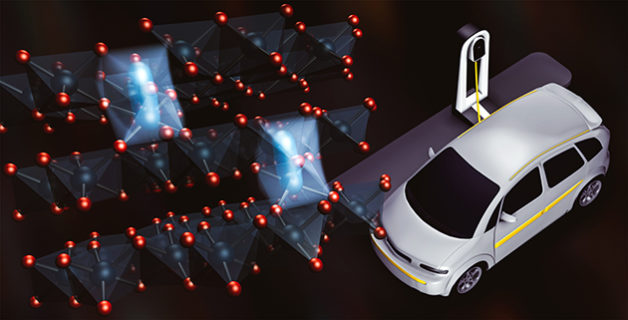
One issue plaguing today’s commercial battery materials is that they are only able to release about half of the lithium ions they contain. A promising solution is to cram cathodes with extra lithium ions, allowing them to store more energy in the same amount of space. But for some reason, every new charge and discharge cycle slowly strips these lithium-rich cathodes of their voltage and capacity.
A new study provides a comprehensive model of this process, identifying what gives rise to it and how it ultimately leads to the battery’s downfall. Led by researchers from the Department of Energy’s Lawrence Berkeley National Laboratory (Berkeley Lab), Stanford University, and SLAC National Accelerator Laboratory, it was published this week in Nature Materials.
“This research addressed a lot of misconceptions in the field,” said study lead William Gent, a Stanford University Siebel Scholar and winner of an Advanced Light Source and Molecular Foundry Doctoral Fellowship at Berkeley Lab. “There’s a long way to go, but now we have a foundational understanding of the properties that lead to this process that’s going to help us harness its power rather than just stab at it in the dark.”
Soaking it up
The cycling of lithium through a battery is like a sponge relay, a staple of picnics and Fourth of July barbecues that challenges participants to transfer water from one bucket to another using only a sponge. The more absorbent the sponge, the more water can be squeezed into the second bucket.
Lithium-rich battery cathodes are like super-absorbent sponges, able to soak up nearly twice as many lithium ions as commercial cathodes, packing as much as twice the energy into the same amount of space. This could allow for smaller phone batteries and electric vehicles that travel farther between charges.
Most lithium ion battery cathodes contain alternating layers of lithium and transition metal oxides – elements like nickel or cobalt combined with oxygen. In commercial batteries, every time a lithium atom leaves the cathode for the anode, an electron is snagged from a transition metal atom. These electrons create the electrical current and voltage necessary to charge the material.
But something different happens in lithium-rich batteries.
“An unusual feature of lithium-rich cathodes is that the electron comes from the oxygen rather than the transition metal,” said Michael Toney, a distinguished staff scientist at SLAC and a co-author of the paper. “This process, called oxygen oxidation, enables cathodes to extract about 90 percent of the lithium at a high enough voltage that it boosts the energy stored in the battery.”
Falling apart
But imagine in the sponge relay that with every subsequent soak, the structure of the sponge changes: the fibers stiffen and bundle together, eating up the empty space that makes the material so efficient at absorbing water. Oxygen oxidation does something similar. The authors’ previous study showed that every time lithium ions cycle out of the cathode into the anode, some transition metal atoms sneak in to take their place and the atomic structure of the cathode becomes a little messier. The layered structure essential to the cathode’s performance slowly falls apart, sapping its voltage and capacity.
In this new study, the researchers showed that this is because yanking the electron from oxygen makes it want to form another bond and transition metal atoms have to move around to accommodate that bond, changing the atomic structure.
Harnessing the effect
Toney said it took the combination of theory and many experimental methods, done at Berkeley Lab’s Advanced Light Source (ALS) and Molecular Foundry as well as SLAC’s Stanford Synchrotron Light Source (SSRL), to disentangle this complicated problem.
This combination allowed the team to conclusively demonstrate the strong driving force behind changes in the cathode’s bonding configuration during oxygen oxidation. The next step, Toney said, is to find ways to produce those changes without totally disrupting the cathode’s crystal structure.
The ALS, the Molecular Foundry, and SSRL are DOE Office of Science user facilities. This research was supported by the DOE offices of Science and Energy Efficiency and Renewable Energy Office of Vehicle Technologies, Battery Materials Research Program.