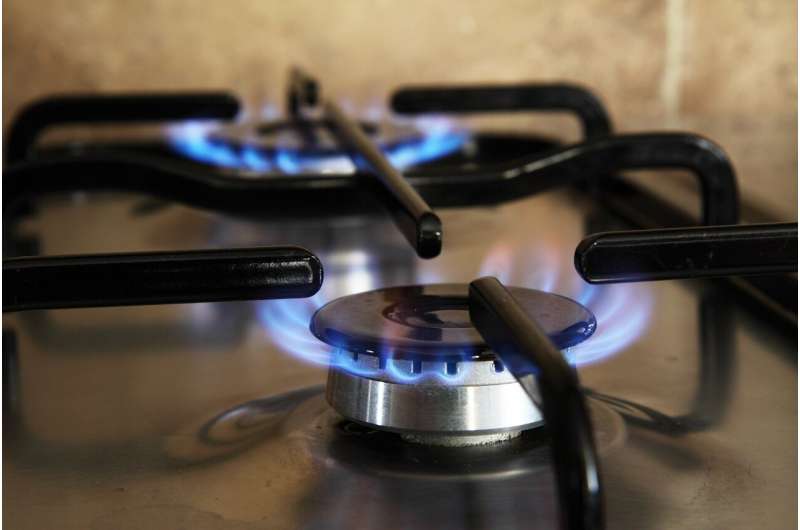
Japan’s Nissan Motor Co Ltd has developed a new technology to halve the cost of recycling rare earths used in magnet motors for electric vehicles (EVs), the company said on Friday.
With tension simmering between China and the United States, automakers are trying to reduce their reliance on a key driver of the EV revolution – permanent magnets that power electric engines, as most are made of rare earth metals from China.
Automakers are also concerned about huge price swings of the metals and environmental damage in the supply chain.
Nissan, collaborating with Katsunori Yamaguchi, a professor at Waseda University, established a new recycling technology to recover rare earth compounds in high purity and efficiency without dismantling the motor, which is the conventional way.
Permanent magnet motors – using rare earths such as neodymium and dysprosium – naturally have magnetic force. These are at the heart of many electric motors, powering the rotor of the drivetrain.
With the new technology in a dry refining method, Nissan melts the rotors in a furnace above 1,400 Celsius, extracts them as an oxide liquid, and then separates them to extract the rare earths.
The new method will shorten the processing time to about 4 hours from 8 hours now and halve the recycling cost, Kazuhiro Ogawa, senior manager at Nissan, told reporters.
Nissan will continue experimenting with larger scale facilities, with an aim to make the process commercially viable in the mid-2020s.
“Reducing the use of rare earths is a key challenge as the resources are unevenly distributed, prices fluctuate depending on supply-demand balance, and the mining and smelting process has an impact on ecosystems,” Ogawa said.
Nissan, which has been cutting the use of heavy rare earths at the design stage and recycling them, will aim for zero dependence on newly extracted resources in future, he said.
In their ongoing effort to make carbon capture more affordable, researchers at the Department of Energy’s Pacific Northwest National Laboratory have developed a method to convert captured carbon dioxide (CO2) into methane, the primary component of natural gas.
By streamlining a longstanding process in which CO2 is converted to methane, the researchers’ new method reduces the materials needed to run the reaction, the energy needed to fuel it, and ultimately, the selling price of the gas.
A key chemical player known as EEMPA makes the process possible. EEMPA is a PNNL-developed solvent that snatches CO2 from power plant flue gas, binding the greenhouse gas so it can be converted into useful chemicals.
Earlier this year, PNNL researchers revealed that using EEMPA in power plants could slash the price of carbon capture to 19 percent lower than standard industry costs—the lowest documented price of carbon capture. Now, in a study published Friday, August 21 in the journal ChemSusChem, the team reveals a new incentive—in cheaper natural gas—to further drive down costs.
When compared to the conventional method of methane conversion, the new process requires an initial investment that costs 32 percent less. Operation and maintenance costs are 35 percent cheaper, bringing the selling price of synthetic natural gas down by 12 percent.
Methane’s role in carbon capture
Different methods for converting CO2 into methane have long been known. However, most processes rely on high temperatures and are often too expensive for widespread commercial use.
In addition to geologic production, methane can be produced from renewable or recycled CO2 sources, and can be used as fuel itself or as an H2 energy carrier. Though it is a greenhouse gas and requires careful supply chain management, methane has many applications, ranging from household use to industrial processes, said lead author and PNNL chemist Jotheeswari Kothandaraman.
“Right now a large fraction of the natural gas used in the U.S. has to be pumped out of the ground,” said Kothandaraman, “and demand is expected to increase over time, even under climate change mitigation pathways. The methane produced by this process—made using waste CO2 and renewably sourced hydrogen—could offer an alternative for utilities and consumers looking for natural gas with a renewable component and a lower carbon footprint.”
Calculating costs and capturing carbon
To explore the use of EEMPA in converting CO2 to methane, Kothandaraman and her fellow authors studied the reaction’s molecular underpinnings, then assessed the cost of running the process at scale in a 550-megawatt power plant.
Conventionally, plant operators can capture CO2 by using special solvents that douse flue gas before it’s emitted from plant chimneys. But these traditional solvents have relatively high water content, making methane conversion difficult.
Using EEMPA instead reduces the energy needed to fuel such a reaction. The savings stem partly from EEMPA’s ability to make CO2 dissolve more easily, which means less pressure is needed to run the conversion.
The authors’ assessment identified further cost savings, in that CO2 captured by EEMPA can be converted to methane on site. Traditionally, CO2 is stripped from water-rich solvents and sent off site to be converted or stored underground. Under the new method, captured CO2 can be mixed with renewable hydrogen and a catalyst in a simple chamber, then heated to half the pressure used in conventional methods to make methane.
The reaction is efficient, the authors said, converting over 90 percent of captured CO2 to methane, though the ultimate greenhouse gas footprint depends on what the methane is used to do. And EEMPA captures over 95 percent of CO2 emitted in flue gas. The new process gives off excess heat, too, providing steam for power generation.
Making more from CO2
The chemical process highlighted in the paper represents one path among many, said Kothandaraman, where captured CO2 can be used as a feedstock to produce other valuable chemicals.
“I’ll be glad when I can make this process work for methanol as efficiently as it does for methane now,” she said. “That’s my long-term goal.” Methanol has many more applications than methane, said Kothandaraman, who has sought to uncover the catalytic reactions that could produce methanol from CO2 for roughly a decade. Creating plastics from captured CO2 is another route the team plans to explore.
“It’s important that we not only capture CO2, but find valuable ways to use it,” said Ron Kent, Advanced Technologies Development Manager at SoCalGas, “and this study offers a cost-effective pathway toward making something valuable out of waste CO2.”