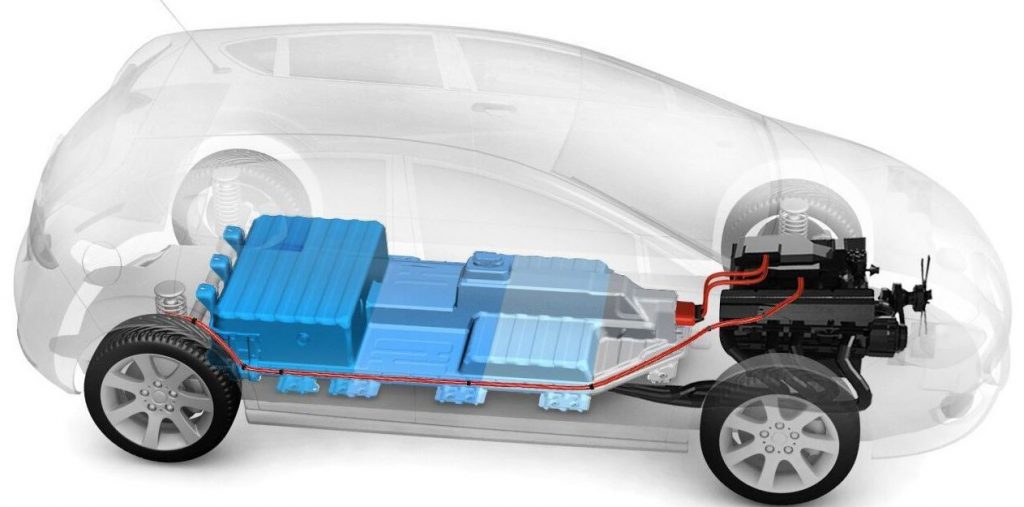
Automobile companies, such as Ford, General Motors and BMW, are investing in the development of large, solid-state batteries to power the electric vehicles (EVs) they are designing for 2030.
That was one message of John Bates, a retired Oak Ridge National Laboratory chemist and battery consultant, in a recent lecture via Zoom to Friends of ORNL. Bates and his group at ORNL pioneered the development of some of the first solid-state, micro-sized batteries in the 1990s.
They made a layered, paper-thin battery using a solid electrolyte Bates discovered in 1991 called lithium phosphorus oxynitride (LiPON). Today several companies make solid-state, thin-film batteries based on the ORNL prototypes for use in implantable medical devices, smart cards, radio frequency identification tags, sensors and other micro technologies.
Lithium-ion batteries used in smartphones, smart tablets, laptops and today’s electric vehicles use liquid organic electrolytes, which perform well at a relatively low cost, Bates said. Unlike solid electrolytes, liquid electrolytes have two problems: they are toxic and can burst into flames. Such fires and explosions, which Bates referred to as “thermal runaway,” result when repeated charging and discharging causes lithium dendrites (crystalline masses) from one battery terminal to grow through the electrolyte and contact the opposite terminal, causing a hazardous short circuit.
An electrolyte is the substance in a battery that separates the anode (negative terminal) from the cathode (positive terminal). Electrons from the anode move through an external circuit while lithium ions travel through the electrolyte and into the lithium ion vacancies in the cathode created by the prior charge step. Because thin-film batteries always contain excess lithium, the battery will continue to produce electricity until the cathode’s vacancies are filled.
In a typical thin-film battery fabricated on a non-conducting ceramic plate, the cathode made of lithium cobalt oxide is deposited onto a current collector (gold over titanium). The plate is then heated in an oven at about 700 degrees Celsius for an hour to make the cathode compound crystalline. The LiPON electrolyte is deposited on the cathode, and then the LiPON is topped with the metallic lithium anode. All the layers are encapsulated in a packaging material, the first of which was developed at the Oak Ridge Y-12 National Security Complex in the 1990s.
The ORNL technology was licensed to numerous companies. One licensee was Front Edge Technology Inc., a California company started in 1994 that claims to make the world’s thinnest rechargeable battery, which is only 0.1 millimeter thick.
Bates, who had worked this century for the startup Oak Ridge Micro Energy, told FORNL that he and his colleagues there provided thin-film battery prototypes to an Israeli startup company to power an implantable arterial medical device. The tiny package containing the device and battery was to be inserted into a lung artery in patients with congestive heart failure to monitor them in real time and provide a warning if a cardiac event is imminent.
“We made a battery that fit in the Israeli device package,” Bates said. “I sent several prototypes to my contact at the Israeli company, but the shelf life of a charged micro-battery with so little capacity was never long enough to warrant their use in medical devices during production. Over the years, our prototype batteries were developed for other implantable devices including defibrillators and neural stimulators for pain control.”
What auto companies wish to do is to scale up the thin-film battery technology to make large enough solid-state batteries to power electric vehicles. Utilities also want large solid-state batteries to store the excess energy produced by wind turbines and solar panels so the batteries can keep electricity flowing through the grid when the sun doesn’t shine and the wind doesn’t blow.
Bates said the daunting problem for car companies and utilities lies in the manufacturing challenge. Can a fire-resistant, solid-state battery stack be assembled that performs with higher energy density at roughly the same cost as today’s elecrtric vehicles and utility batteries, which are less safe because they use liquid electrolytes?
Bates told the FORNL audience that he came up with the idea for LiPON as a solid electrolyte when he learned the glasses used for underwater cables were “nitrided” — heated in the presence of a nitrogen-containing material to increase their chemical durability.
“So, we made LiPON by sputtering lithium orthophosphate in a pure nitrogen atmosphere,” he said.
Bates received a number of awards at ORNL for his discovery.
The recipients of the 2019 Nobel Prize in Chemistry were three battery researchers, Bates said. They are M. Stanley Whittingham (Binghamton University, State University of New York), John B. Goodenough (University of Texas at Austin), and Akiro Yoshino (Asahi Kasei Corporation, Tokyo, Japan). They were honored for their development of lithium and lithium-ion batteries.
Knowing how difficult it is to build new batteries and scale them up, Bates cautioned his audience to be careful if anyone is considering investing in new companies that promise better batteries.
In answer to a question, he agreed that it would be desirable to recycle lithium from used lithium-ion batteries for reuse in future batteries, but he suggested that such recycling might not be feasible because of the high cost.