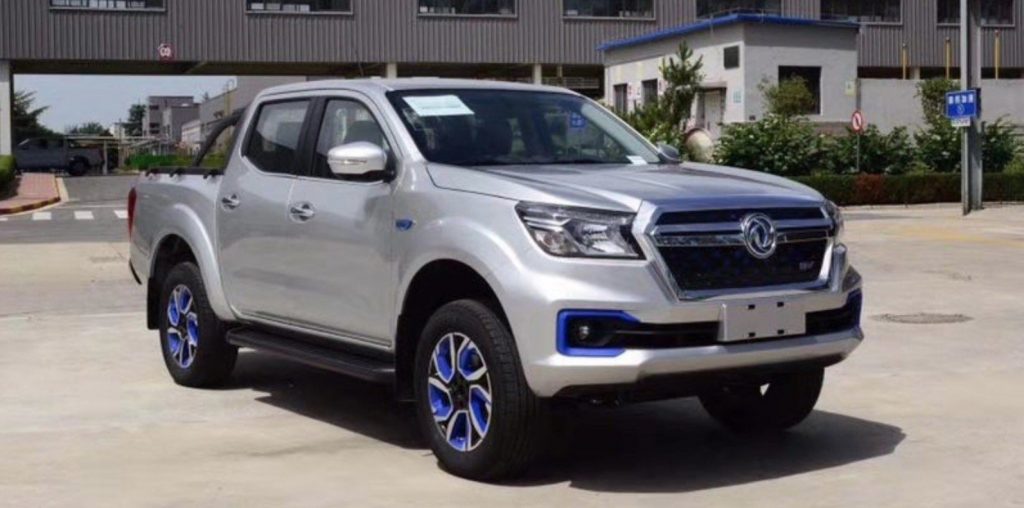
While we are impatiently waiting for Tesla, Rivian, and others to bring their electric pickup trucks to market here in North America, China is already getting some.
Nissan is launching a new electric pickup truck through a Dongfeng joint venture in China: the Dongfeng Rich 6 EV.
With its aggressive zero-emission mandate, China has forced automakers to accelerate their deployment of all-electric vehicles in the country.
Several of them are now making EVs just for the Chinese market.
Nissan is one of them and with their joint venture with state-owned Dongfeng, they are launching an all-electric version of their Dongfeng Rich pickup truck.
The gasoline version is based on Nissan’s pickup truck platform and it has been converted to an electric powertrain.
The Dongfeng Rich 6 EV is relatively compact (5290/1850/1790 wth a 3050 wheelbase) wth a small bed (1510/1562/475) and it has curb weight of 1,983 kg (4,370 lbs) with a max load of 490 kg (1,080 lbs).
Its double cabin can seat 5 people.
As for the powertrain, it is equipped with a single 160 hp/420 Nm electric motor and a 68 kWh battery pack.
Dongfeng claims a range of 403 km (250 miles) on a single charge, but that’s using the NEDC standard, which is generally nowhere near a normal use case.
The top speed is 110 km/h (68 mph) and the company says that it is fast-charging capable. Without confirming the max charge rate, Dongfeng says that it takes 45 minutes to get to 80% state-of-charge.
The Dongfeng Rich 6 EV should hit the market as soon as next month. The price is unknown, but it is expected to be extremely cheap — maybe even 130,000 yuan ($18,900 USD) after subsidies.