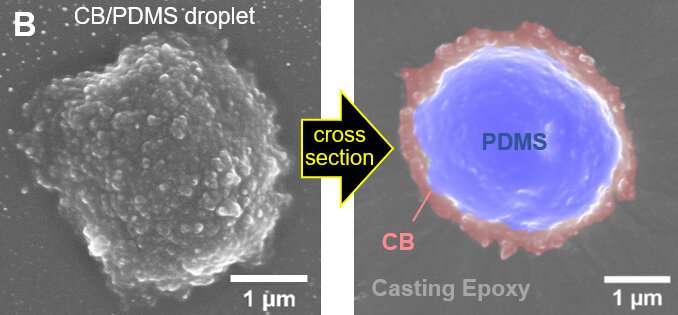
A growing number of companies and research groups worldwide are now developing compliant sensors based on composite materials, which can have a wide range of possible applications. Composite materials, those made of two or more substances, often have unique and advantageous properties that differ from those of their individual components.
Past studies have found that composite materials containing polymer matrices and conductive fillers are particularly promising for the development of compliant sensors, as they can be printed on large scales. A key advantage of sensors made of this class of materials is that they can be integrated in geometrically complex or flexible systems, such as wearable devices and soft robots.
Researchers at Yale University have recently introduced an approach that could enable the sustainable manufacturing of compliant sensors for soft robotics applications. This approach, presented in a Science Robotics paper, involves the use of an ethanol-based Pickering emulsion that spontaneously coagulates, creating a conductive composite that can easily be printed on soft robotic systems.
“Printing composite materials generally entails the use of solvents, such as toluene or cyclohexane, to dissolve the polymer resin and thin down the material to a printable viscosity,” the researchers wrote in their paper. “However, such solvents cause the swelling and decomposition of most polymer substrates, limiting the utility of the composite materials. Moreover, many conventional solvents are toxic or otherwise present health hazards.”
Aware of the challenges encountered when trying to print composite materials using solvents, the researchers at Yale devised a new approach that could enable the manufacturing of sensors in a more efficient and sustainable way. The strategy they developed is based on the use of an ethanol-based Pickering emulsion that coagulates spontaneously, creating a conductive composite that can be printed into different types of sensors.
“The Pickering emulsion consists of emulsified polymer precursors stabilized by conductive nanoparticles in an ethanol carrier,” the researchers wrote in their paper. “Upon evaporation of the ethanol, the precursors are released, which then coalesce amid nanoparticle networks and spontaneously polymerize in contact with the atmospheric moisture.”
Once they delineated their new sensor manufacturing strategy, the researchers printed the self-coagulating Pickering emulsion into a number of polymeric systems, including traditional textile materials and soft actuators. The conductive substance they used gave these systems sensing capabilities, resulting in different types of compliant sensors.
So far, the researchers have used their manufacturing approach to create composite-infused kinesiology tape, knee pads and cotton gloves. They also applied the same strategy to fabricate soft robotic skins, dubbed OmniSkins, by printing the the conductive emulsion on muslin fabric and attaching actuators on it.
In preliminary tests, the Pickering emulsion-based sensing systems developed by the researchers achieved a remarkable strain sensitivity and negligible hysteresis, which are highly desirable properties for most wearable technologies and soft robotics applications. In the future, the new manufacturing strategy introduced in this recent paper could enable more sustainable development of innovative and highly performing sensing technologies, including soft robotic skins and items of clothing with sensing capabilities.