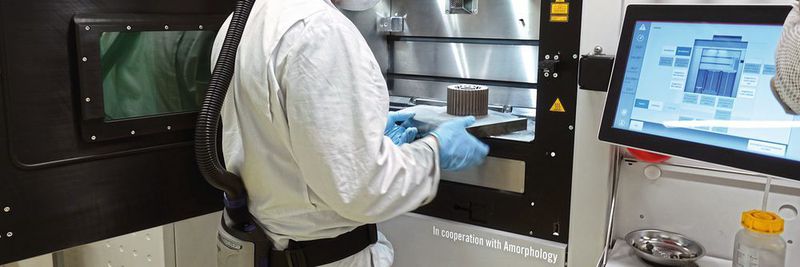
Amorphous metals are highly elastic, hard, light and at the same time break-resistant. Thus they are ideal materials for high-tech applications. In additive manufacturing, these advantages can be used in a completely new way.
Whether in aerospace, medical technology or e-mobility: Modern high-tech applications place enormous demands on today’s materials, for example to produce wear-resistant drive components and gears, stable suspensions or membranes for injection nozzles. In complex designs and extremely light construction methods, conventional manufacturing processes quickly reach their limits. Additive manufacturing enables the production of tailor-made solutions that fulfil a huge number of new requirements.
Atomic Chaos as a Solution for Various High-Tech Applications
Amorphous metals are versatile and combine properties that have previously been mutually exclusive. This makes them extremely strong and highly elastic at the same time. In addition, they have very good spring properties, are extremely corrosion-resistant and shock-absorbing. The reason for this is their disordered, non-crystalline structure. The challenge in the production and processing of amorphous metals is the fact that the atoms in the melt retain their amorphous arrangement during solidification. These metals are therefore frozen melts, which are also referred to as metallic glasses. “The high strength of the material makes it possible to modify the design of components and make them thinner or smaller than is possible with standard materials,” explains Valeska Melde, Marketing & Sales Manager at Heraeus Amloy. An enormous advantage for heavy-duty parts that often wear out – such as gear parts.
A further advantage is the low density of amorphous metals, which is below that of steel. This reduces weight – one of the biggest challenges for innovations in e-mobility and aerospace. “Our developments in amorphous metals are a major driver for increasing ranges in e-mobility and reducing energy costs in the aerospace industry,” says Valeska Melde. In addition to their low weight, amorphous metals offer another decisive advantage for the aerospace industry: unlike other metals, they do not become brittle at extremely low temperatures (low temperature ductility) and are therefore particularly suitable for extreme environments. Thanks to their high creep resistance, amorphous metals can also be used to produce light, small and stable rotor elements, for example for drones.
High-Tech Material from the 3D Printer
In addition to the injection molding of amorphous metals, Heraeus also manufactures amorphous components by means of 3D printing . “Additive Manufacturing allows the production of larger components with complex geometries that could not be produced with conventional methods before,” explains Jürgen Wachter, head of the Heraeus Amloy business unit. High-purity, spherical, amorphous powders based on zirconium or copper are specially optimized for additive production in selective laser melting (SLM). Heraeus Amloy is currently working on the development of a titanium-based alloy that can also be used in additive production. The combination of very low weight with optimized component geometry is especially useful in lightweight design. A platinum-based alloy from Heraeus Amloy is of particular interest to the jewelry industry because, unlike pure platinum, it is scratch-resistant.
The powders for laser melting in additive manufacturing are produced by atomization in the EIGA (Electrode Induction Melting Inert Gas Atomization) or VIGA (Vacuum Inert Gas Atomization) process. These powders can be processed on all SLM machines. Heraeus Amloy determines the corresponding parameters for the respective customer and, together with partners, also optimizes the printers for amorphous components. Just like standard materials, amorphous components can also be reworked – depending on the desired surface structure or shape. The alloys can be ground, blasted, polished or machined.